Natural Ventilation Comes Full Circle
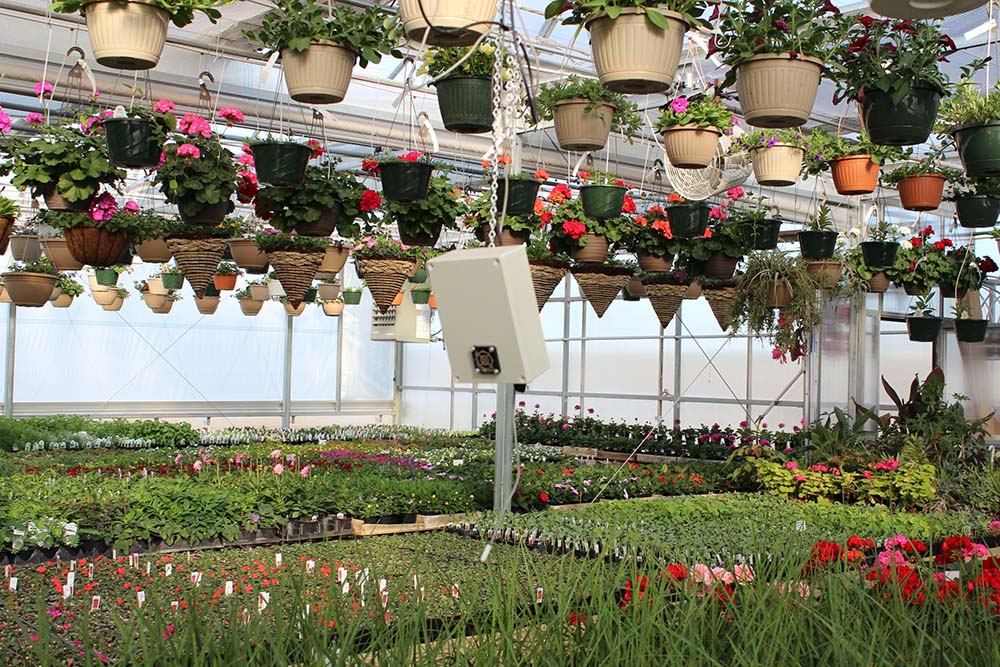
The greenhouse industry is mixing the old with the new these days, combining low tech natural ventilation of old, with high tech solutions for the 21st Century. This trend is saving energy and labor while producing quality products with fewer pesticides and fertilizer. This relatively new era of greenhouse growing will provide growers with opportunities as well as challenges as growers seek to keep up with the advances in technology.
Going full circle
In the early days of covered growing, greenhouse and high tunnel growers relied on natural ventilation with manual controls to cool the greenhouse. All greenhouses built before 1950 had some form of vents and louvers to allow excess heat to escape and cooler air to enter. However, with the advent of polyethylene that covered the entire growing structure, placing vents on the roof was no longer feasible (Bartok, 2014).
As a result, the industry adopted the concept of ventilation that greenhouse growers are familiar with and, and today many are still using: fan and louver ventilation, which draws air through the entire length of the greenhouse structure. They turned away from natural ventilation and into fan ventilation as a means to foster more control over the greenhouse environment, shelving, to some extent, the concept of natural ventilation.
Fan ventilation for controlling the greenhouse environment has been effective to a point. However, it requires substantial energy inputs to run the fans, and greenhouse temperatures are distributed unevenly which can result in temperature fluctuations within the structure and less uniform growth.
High tech advances
In the last five years the industry has advanced in leaps and bounds, combining the energy saving benefits of natural ventilation with high tech digital automation and environmental controls that include touch screen commands.
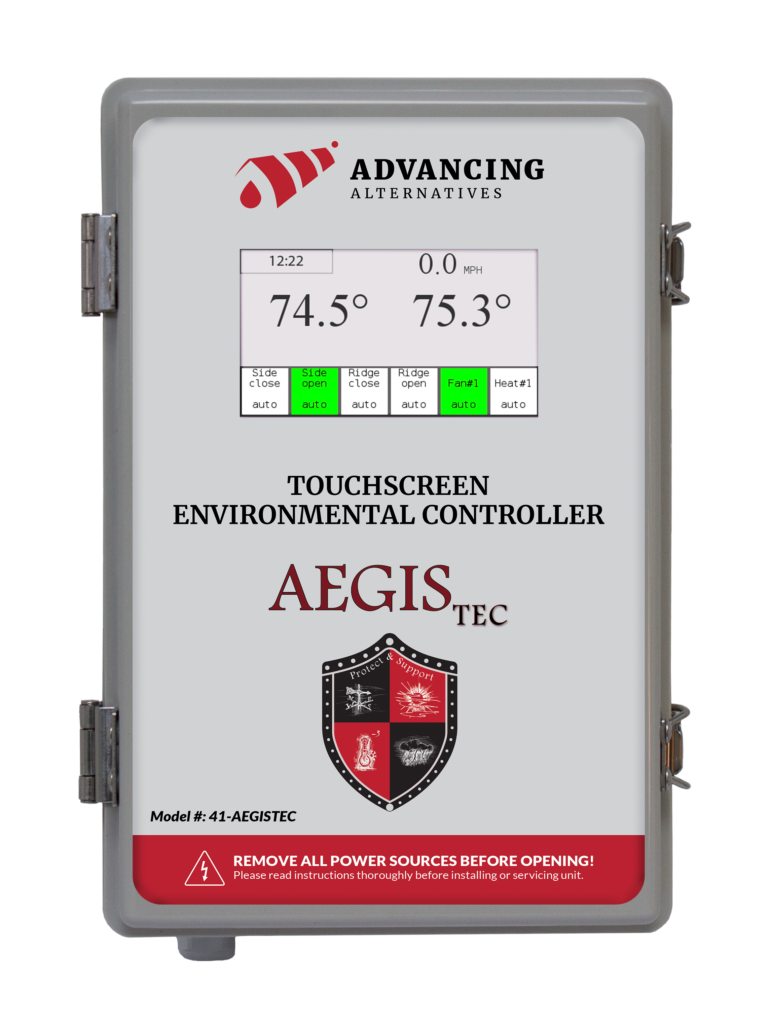
Small, lightweight, low voltage 8-15 pound motors, used to roll-up the sides of the greenhouse or high tunnel, have revolutionized the industry, replacing tube motors, once considered an innovation in the industry, that would overheat and burn out. Roll-up curtains with tight seals at the bottom, developed by Advancing Alternatives, helped to make natural ventilation work for growers.
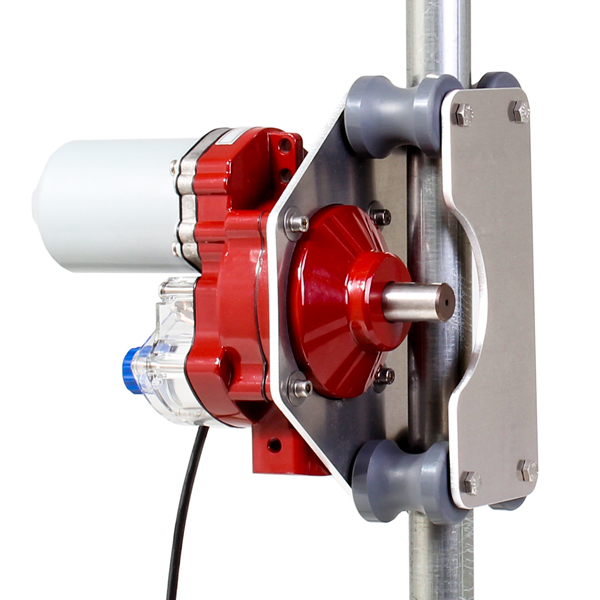
State of the art greenhouses and high tunnels of today can use fans during inclement weather and when high wind situations exist. Some environmental control systems will allow for high cutoff set-points to shut off the fans, effectively conserving energy while continuing to provide an optimal growing environment.
Understanding natural ventilation
The concept of cooling a greenhouse with thermal buoyancy and wind can be traced back to the beginning of the controlled environment movement (Bartok, 2014). Roof and sidewall ventilation is the backbone of natural ventilation, which operates under the principle that heat is removed by a pressure difference created by wind and temperature gradients. According to the research (Bartok, 2014), in a well designed and situated greenhouse, a wind speed of 2-3 miles/hour provides 80% or more of the ventilation needed.
Wind speeds of 1 mph are adequate to keep the inside temperature within two degrees of the outdoor temperature (Bartok, 2015). And weather records indicate that there are very few days that the wind is less than one mph, especially when the outdoor temperature is above 80 degrees Fahrenheit.
Natural ventilation not only cools the inside of a greenhouse during warm, sunny days, but also supplies carbon dioxide vital for the plant’s photosynthesis and replaces moist air with drier air, preventing a buildup of humidity that can be a prelude to fungal diseases.
With a natural ventilation configuration, wind passing over the roof creates a vacuum and sucks the heated air out of the roof vent. When the sidewalls are open, cool replacement air enters and drops to the floor level. If the sidewall vents are closed, cool air enters the bottom of the roof vent and the warm air escapes out the top (Bartok, 2014).
Roof and side vents: the backbone of natural ventilation
It’s important to note that roof and side vents on conventional greenhouses need to be large enough to get good air movement (Bartok, 2014). The American Society of Agricultural Engineers recommends that the combined sidewall vent area should equal the combined ridge vent area and each should be 15-20% of the floor area.
Greenhouses should be oriented so that the prevailing summer winds blow over the ridge, which will create a vacuum on the leeward ridge vent. Proper sizing, orientation to the wind, and operation can provide better control than with HAF (Bartok, 2014).
As mentioned in last month’s blog post, energy savings can be realized with natural ventilation even in a greenhouse that utilizes cooling pads. The sealed curtains developed by Advancing Alternatives lock-seal at the bottom to allow cooling fans to work efficiently. Natural ventilation, utilizing side and roof vents, can be deployed when it’s cooler.
Fortunately, conventional greenhouses and high tunnels currently relying on mechanical ventilation can be retrofitted with sidewall curtains and environmental controls to take advantage of the energy and labor saving benefits of natural ventilation .
Advantages of open roof ventilation
There are several advantages to rack & pinion roof ventilation; whether used on a high tunnel or gutter connect house they are a valuable asset for greenhouse growers:
• The temperature inside the greenhouse can be maintained within a degree or two of the outside temperatures on warm days, with little to no energy needed.
• Plants can be hardened off in the spring by opening the roof on favorable days, saving the labor of moving plants outside.
• Energy costs are reduced; fans can use from 0.5-1 kilowatt-hour/sqft/year.
• Reduced irrigation due to more uniform temperatures.
• Side vents will allow cool air to enter the greenhouse even when wind or rain prevent the roof from being opened.
Source: “Natural Ventilation in Greenhouses,” University of Connecticut,” 2014.
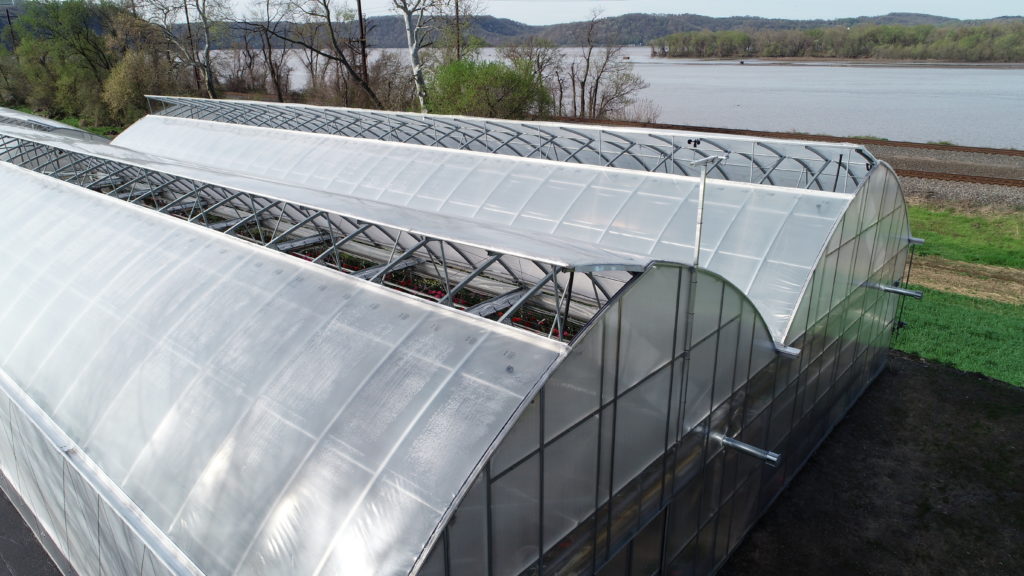
The future demands it
A look into the future punctuates the need to turn to natural ventilation with automated controls. The United Nations predicts the world’s population to swell to 9 billion by 2050, with two-thirds of these people concentrated in urban areas. Greenhouses will increasingly be near or within these population centers. The need for energy efficiency and conservation will only be compounded. Securing the supply chain with fresh fruits and vegetables in this new scenario will be an overwhelming challenge (Shamshiri et al., 2018 ).
In the above-referenced study, Shamshiri and his colleagues conclude that the greenhouse of the future will be “smart controlled environments that benefit from natural resources for eliminating deleterious external conditions.” The ultimate objective, they say, is for the highest possible yields at the lowest cost, which they contend will be best achieved with natural ventilation with automated controls. Advances in the future will be along the lines of wireless sensor networks (WSN), internet of things-based platforms (IoT-based) and artificial intelligence (Shamshiri et al., 2018).
Controlling variables
The high tech options available now and in the future require an upfront investment of capital that should offer good ROI. These high tech monitoring systems and automation will control the variables that affect plant health and productivity in high tunnels, greenhouses and the “plant factories” of the future (Shamshiri et al., 2018). By continuing to study and increase our knowledge of the different variables that affect plant growth growers can become more efficient and profitable.
The efficient greenhouse requires environment control for air quality, disease reduction, pest control and nutrient and water uptake (Shamshiri et al., 2018).
Temperature control
Perhaps the most important variable to control in covered growing is the temperature. Uniform temperatures in the greenhouse will increase the likelihood of uniform cropping, among other things. Greenhouses trap solar radiation, which is a good thing, however, if it gets too high or even slightly above the desired temperature, plants will transpire excessively, requiring more water inputs, which is particularly problematic in drought-prone areas.
High temperatures coupled with dry air can also encourage plant pests, such as mites. Conversely, prolonged temperatures that are too cool can have detrimental effects on plants, more so when they are in the flower development stage–for ornamental flowers– and fruit set and development stage in vegetables and fruit (Bakker, 1995). Natural ventilation, utilizing sidewalls and roof vents, controlled via automated climate controls, will help ensure even temperatures throughout the greenhouse and can do so better than a mechanical system.
Humidity control
Humidity will quickly build-up in a greenhouse or high tunnel if there is no way to ventilate the structure. High humidity, a result of transpiration from plants and the aftermath of overhead watering and irrigation, can create an ideal environment for pathogens, molds, and fungi. Maintaining proper humidity is a component of an integrated pest management (IPM) strategy (UMassExtension, 2015). Automated ventilation and climate controls that regulate humidity can ensure the proper humidity level for a particular crop.
Carbon dioxide and oxygen
As you no doubt remember from your high school biology classes, plants breathe in carbon dioxide and release oxygen. This is critical for the energy cycle we call photosynthesis. Plants also breathe in oxygen, which helps support good root growth. A properly configured ventilation system, with side and roof vents, allows plenty of fresh air to displace stale air.
Proper ventilation has other benefits, including drying off leaf surfaces after overhead watering, strengthening the cell walls of plants, as an aid in plant pollination, and to prevent the growing medium from becoming saturated, which could set the stage for root damage and a favorable environment for fungus gnats.
Welcome to a new era
In closing, we’ve entered a new era in greenhouse and high tunnel growing. The population is increasing, and more food and plants will be grown in less space, close to and within urban population centers. Natural ventilation with automated controls will most likely lead the charge as the most efficient, cost-effective and environmentally friendly way to meet the demand for quality edible, ornamental and medicinal plants.
For over 20 years Advancing Alternatives has helped growers keep up with the many innovations in the industry. For more information on how you can equip your greenhouse or high tunnel with low voltage ventilation motors , state of the art climate controls, roof and side vents, and other labor-saving automation, contact the experts at Advancing Alternatives.
Bakker, J.C., “Greenhouse Climate Control: Constraints and Limitations,” Greenhouse Crops Research Station, The Netherlands, 1995.
Bartok, John W. Jr. “Natural Ventilation Guidelines,” Greenhouse Management, Aug. 2015.
Worley, John W. “Greenhouses: Heating, Cooling and Ventilation,” University of Georgia Extension, Published with full review on Dec. 2014.
John W. Bartok, Jr. “Natural Ventilation in Greenhouses,” University of Connecticut,” 2014.
Shamshiri R.R. et al., “Advances in greenhouse automation and controlled environment agriculture: A transition to plant factories and urban agriculture,” 2018.
UMassAmherst, Center for Agriculture, Food and the Environment, “Reducing Humidity in the Greenhouse,” 2015.